These companion 3d designs can be a fun way to decorate
for the harvest season on shelf or in a centerpiece.
Or you can fill them with the dimensional veggies
that are also paper creations to add color and interest.
Large jar measures approx. 3.5” x 3.5” x 6.25”,
and includes the "Have A Ball" side cutout.
Short jar measures approx. 3.5” x 3.5” x 4.5”
and sports the "Sweet Harvest" side cutout.
Assembly is made in jar sections, so each can be cut from
smaller than 12x12 card stock.
Acetate clear panels fill in sides, bottom and corner bevel windows
to make these jars very see-thru.
Make the close fitting lid as top closure,
and add optional fabric circle cinch top
(pattern included in file, specific to these designs).
Silhouette Cameo users will probably be familiar with
their digital tool's ability to cut shapes from fusing-bonded fabric.
NOTE: Construction is identical for large or short jar versions, except for the decorative "phrase" shape (G below) that is unique for each. Photos included in tutorial from both sizes.
CONSTRUCTION:
1. Identify and cut the shapes.
(large is shown here)
A jar body with attached top
B jar body with attached bottom
C bottom reinforcing shape (optional) with base build up rings
D bottle neck
E clear acetate shapes for sides, corners, bottom
F lid shapes: top, rim, rim accent overlay, top ring overlay
G "Have A Ball" phrase shape
2. Prepare the two side jar body shapes by folding on perforations. ALL are inward or "mountain" folds.
3. Join the front/top body shape (shown at left here) and front/bottom (shown right) by overlapping the straight edge to the long flange perforation and gluing in place. Take care to make sure top and bottom defining perforation lines of each match up.
4. Prepare to attach the clear acetate window panels by applying "dry" adhesive strips to each panel section. My recommended product is Kool Tak clear. I have attached a strip in each panel within the defining perforation line, then trimmed it to size. For larger openings I applied strips on four sides. For narrow openings I applied strips only on sides.
For the non-tabbed large window side opening edge, leave the adhesive strip off...
... and apply it to the opposite tabbed side. (This window panel will be inserted AFTER the sides are joined, so the acetate panel will need to attach to the backside of the tab the surface of which will still be exposed to allow the join.)
5. Position and attach ALL window panels except the non-tabbed end large panel.
(Wait until Step 11 for last panel.)
6. Apply your regular paper-to-paper adhesive and join the remaining side seam. Take care to overlap and align all straight edges and perforation lines as accurately as possible.
7. Fold the lower bevel edge sections and tabs back, align straight edge and perforation line, and accurately glue in place.
This is how the jar assembly should look at this stage. Bottom bevel edges seams are joined, but tops are not.
8. Fold the tabs of the bottom inward, apply adhesive, then tuck tabs inside jar side edges to attach. Begin with the edge opposite the connected side, taking care to center and align accurately. Since there is still one side panel "open" (no acetate in place yet), you can still reach in with fingers to help apply targeted pressure.
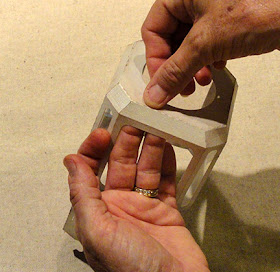
9. Position and attach remaining long side edges, then corner bevel edges.
10. Build up the bottom (to simulate an actual mason jar) by layering and attaching multiple bottom rings. You can assemble the rings away from the jar structure first if preferred, or add them one at a time to the jar's bottom.
11. Insert and attach the final side window panel.
12. Prepare the jar neck shape by folding main shape vertical perforations, inner edge perforation lines and flange lines, and lower, end tabs as inward folds.
13. Apply adhesive at the bottom of each flange segment, then position the bottom edge even with the opposite tab perforation line. Since each tab segment is slightly narrower than the corresponding ,outer surface segment, side edges will not line up exactly. Instead, the flange should align at left edges/corner.
Attach each of the 12 segments this way, but leave the non-tabbed end free until after Step 15.
14. Fold the neck shape into a ring, taking care to overlap the "miter" joint between segments consistently, left over right, etc. It is a small joint that will remain unglued, but the neck will take a better, symmetrical shape if care is taken at this point. You may need to use a pointed tool to help guide the under edge into place.
15. Overlap straight ring end over tab and glue in place. Fold final inner flange into place and glue as previously done for other flanges.
16. Line up ring lower tabs with slots on jar top and gently insert until the ring lower edge is snugly against jar top surface. The slots are cut for a very snug fit, so work around in a series of steps to complete the insertion.
17. On the inside jar top, fold the tabs outward and glue each in place.
18. Fold the jar top tabs inward, then swing the top into place while inserting tabs behind jar side edges. Follow the same procedure as in Step 8 to attach the side opposite the connection first, straight side edge with top tab perforation line, then align and attach the other two long side edges.
19. Fold the bevel edges into place to align with two side edge perforations and one top, then glue in place. Repeat for all four sections.
YOUR JAR ASSEMBLY IS COMPLETE!
20. Prepare the jar lid rim shape by folding bottom flanges up, vertical folds and tabs inward in a manner similar to jar neck (though without miter joints).
21. Fold bottom flanges into place and glue, leaving non-tabbed end unglued until after Step 22.
22. Form the rim shape into a ring, overlap straight edge to tab perf line and glue in place.
Fold the final flange into place and glue.
23. Position the top lid shape by lining up each straight edge with a segment of the rim, then glue tab in place on backside. Join all tabs and edges.
24. Prepare the rim accent shape by folding vertical perforations, end and top tabs inward.
Apply glue to backside of "body" and tabs, then line up with segments of rim/top and attach in place. Attach end with tab, then overlap straight end edge to complete the joining. Top tabs fold back into neat, non-overlapping miters, as shown near right of this image.
25. Position and attach the top ring decor shape.
Place the lid on your jar. The lid is intended to be a snug fit, so it may take a little care to fit it into place.
26. Apply adhesive and carefully position to attach the decorative front shape. The "phrase" shapes for large and short jar designs are relatively interchangeable.
"Have A Ball" was designed for the large jar, shown here.
"Sweet Harvest" was intended for the short jar.
DECORATIVE FABRIC TOPPER
Directions here are for cutting the fabric shape using the Cameo cutting tool. This process may be similar with other tools, but you may wish to run a test if you haven't tried this with your system before.
27. Cut a section of light weight fusible web (not "interfacing" as the Silhouette product might lead you to believe) that is approx. 1/2" larger on each edge than your required cut shape. Apply the fusing to the backside of your fabric cotton print per manufact. instructions. I recommend removing the paper backing before cutting.
28. Smooth the fabric with fusing on its backside onto your cutting mat.
29. Prepare to cut with your machine-specific (per your test) settings. For the Cameo, I use the fabric cotton print settings, but adjust my blade to 5 in the software AND the blade itself. Then send the job to cut.
30. Remove the excess fabric (weed it), and then carefully remove the fabric shape. It doesn't require THAT MUCH care, but it is fabric which is different from paper.
JUST A WORD OF CAUTION: from this point on, the fabric topper is heat sensitive, which is to say that if touched by a hot iron, it will attach itself to whatever is is laying on. Also avoid touching the shiny back (glue) side with hot iron.
31. Use 24-30 inches of twine or string threaded onto a darning needle to attach the cinch string. Insert the needle down-up through the closely-paired holes as shown.
32. Once completely threaded, adjust string so that ends are somewhat even in length. Tie ends in a simple overhand knot to prepare to place it onto the jar top.
33. Center the topper over the jar lid, then carefully cinch in the string, pull up ends to tighten the knot, then tie ends either into a double knot or with bow ends. Trim excess string ends as desired. Adjust the topper downward on the neck as far as possible.
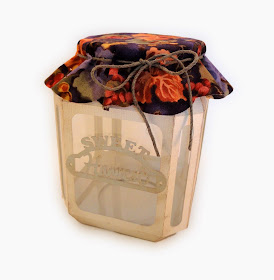
Here is the completed short jar. And a few more gallery images follow.
Short jar spilling its replica pickle contents.
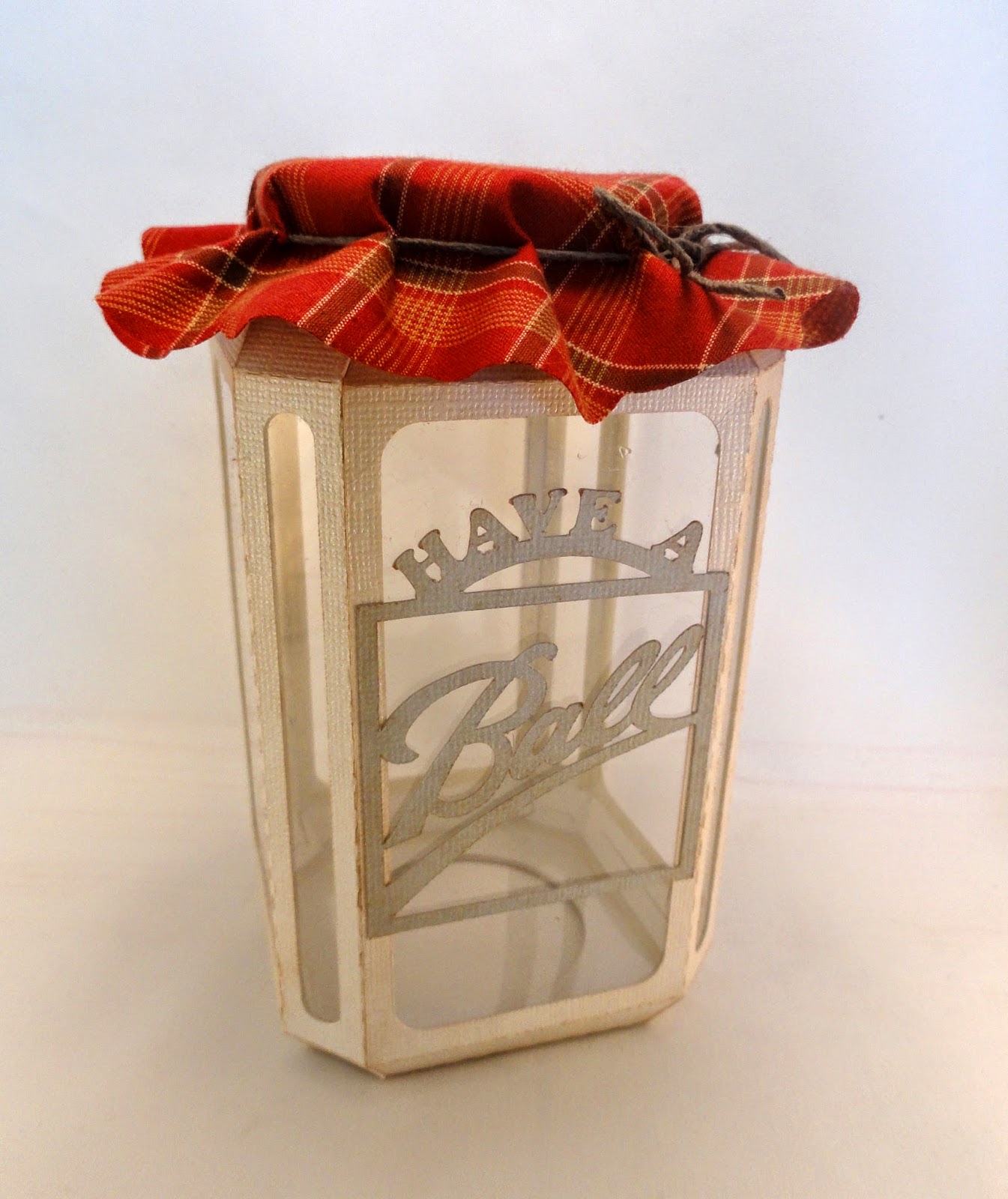
Large jar with topper.
Large jar spilling its contents of replica beets, with and without (in jar) stalk tops.
These are absolutely fabulous. I can't believe how you can turn paper products into something that looks so real! You have such a talent, and I thank you for sharing it with all of us!
ReplyDeleteKudos back to you, and a great genesis idea!
ReplyDeleteWOW Jodi!!! ... I have been waiting for all this to show on the silhouette store and as of today, nothing! :) Ditto on what Beth said
ReplyDeleteJodi, these are fantastic! I can't wait to try these!
ReplyDelete